Lost wax casting dates back over 6,000 years as one of the oldest methods used in making jewelry. Over the years, it‘s now incorporated with newer jewelry production methods, such as 3D printing and CAD software.
In this guide, we will explain everything you need to know about lost wax casting jewelry and how it can be a plus in crafting your jewelry designs.
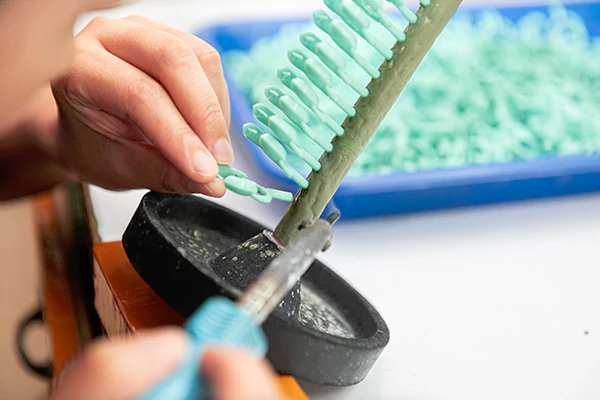
What is Lost Wax Casting Jewelry?
Also known as investment casting, lost wax casting involves making a metal object from a wax model.
Lost wax casting jewelry is a method used to make intricate and detailed jewelry pieces by casting metal into a mold formed from a wax model. It involves designing a mold using wax, which is melted away to result in a cavity. Then, molten metal material is poured into the cavity to create the custom piece.
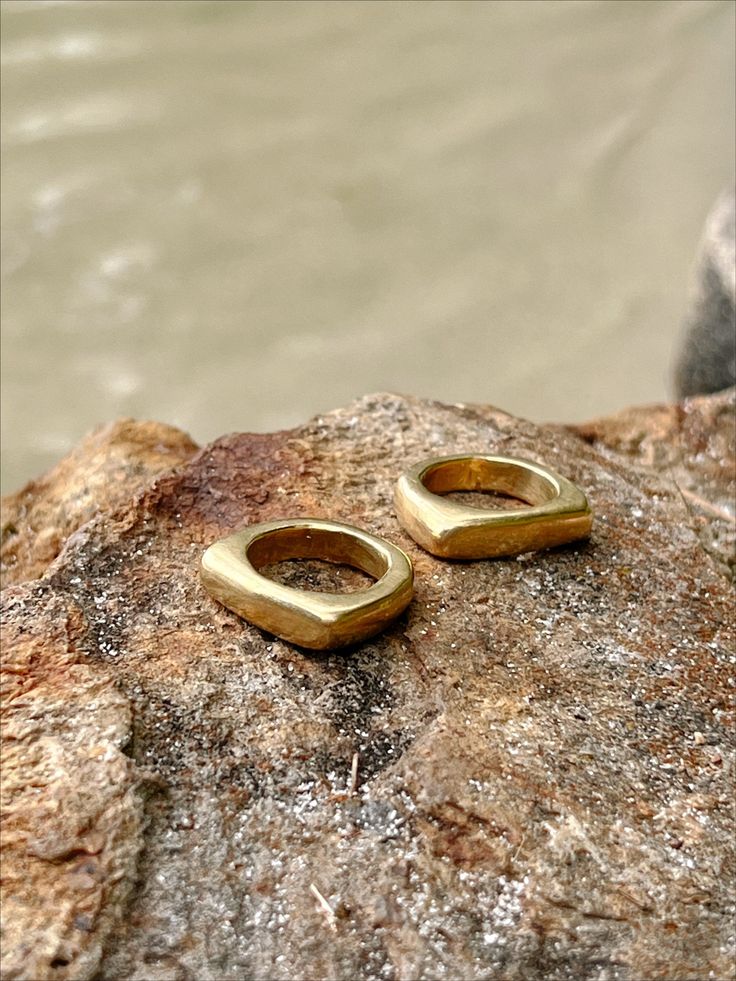
Source: Pinterest
Common Metal for Jewelry Lost Wax Casting
There are several metal materials used for lost wax casting process jewelry, but these are the most common:
- Brass: An alloy of copper and zinc. This material is often used for jewelry that require a gold-like appearance. Brass is durable, affordable, and complements with a warm, yellow hue.
- Bronze: An alloy of majorly copper and tin. This metal is commonly used because of its toughness and vintage look, especially for sculptural and statement jewelry.
- Silver: Can be pure silver (100% silver) or sterling silver (92.5% silver and 7.5% other metals). This material is popularly used for lost wax casting rings with stones because of its malleability, luster, and shine.
- Gold: Can be solid gold (24K) or alloyed with other metals to produce varying gold karats (such as 14K, 18K, or 22K). This material is widely used for making high-end and heirloom jewelry. It’s available in different colors, such as yellow, rose, or white.
The Lost Wax Casting Process
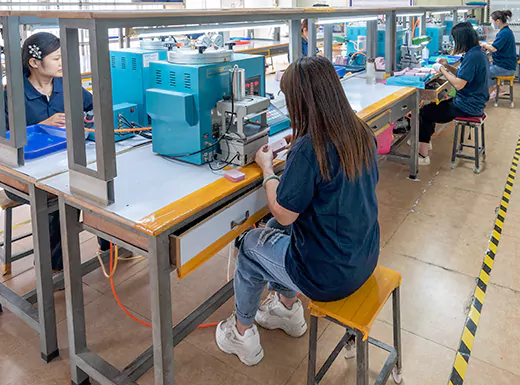
Here’s a lineup of a lost wax casting jewelry manufacturing process:
1. Model-making
Begins with creating a detailed wax model of your desired jewelry. It should be hand-carved precisely to replicate the final piece.
2. Creating a Mold
The wax model is inserted in a mold material to form a solid mold. It must be inserted firmly to capture all the details of the wax model.
3. Wax
The type of wax used must be rightly chosen to glue tightly to the mold. It needs to be high-quality as it determines the final shape of the jewelry.
4. Chasing
This process involves smoothing the surface of the wax model and the mold, ensuring there are no imperfections.
5. Applying Investment Materials
To further harden the mold and make it suitable for the production process, investment material (usually a mixture of plaster and silica) is poured around it.
6. Burnout
The shape is heated in a kiln, making the wax melt and burn out. This results in a cavity with the shape of the desired jewelry piece.
7. Pouring
Molten metal (brass, bronze, silver, or gold) is poured into the cavity. It’s properly poured to fill the cavity, taking on the shape and details of the wax model.
8. Devesting
Leave the metal for a few minutes to cool and solidify. Afterward, remove the mold to reveal the metal casting.
9. Finishing
To have wax-free jewelry, the metal casting must be cleaned. Any material attached to its body is removed, the surfaces are smoothened, and it’s polished for a fine look.
10. Stone Setting
For jewelry pieces designs that include gemstones, the stones are set after the metal casting is cleaned and polished.
Types of Stone Setting for Lost Wax Casting Jewelry
There are two major techniques of setting gemstones in lost wax casting jewelry manufacturing. They are Prong Setting and Channel Setting.
- Prong Setting: Uses prongs (small metal claws) to hold the gemstone firmly in jewelry. Oftentimes, 4 to 6 prongs are used, allowing a lot of light to pass through the gemstone. This makes the stone appear brighter and more beautiful, hence why this technique is used for classic jewelry pieces.
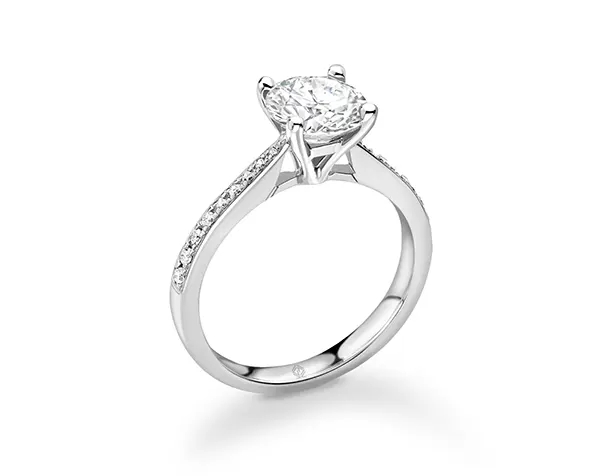
- Channel Setting: Usually used when multiple stones are to be set in jewelry. The stones are placed together in a channel with no metal separating them. The channel wall holds the gemstones in place. This setting technique offers a smooth and sleek look with no prong that can hook your clothes.
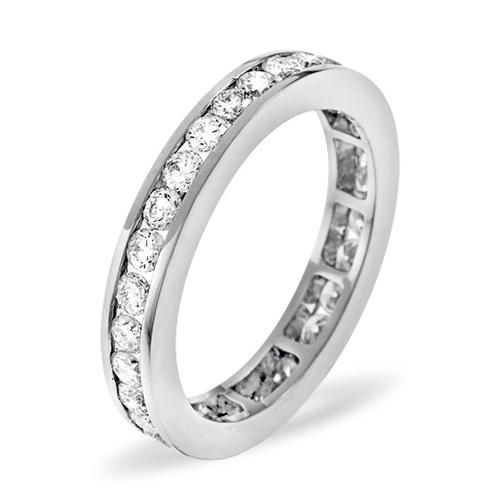
Source: Pinterest
Advantages of Jewelry Lost Wax Investment Casting
- Creativity: Lost wax casting jewelry manufacturing allows jewelers to create intricate and detailed designs precisely. Through wax modeling, highly complex and unique pieces can be created.
- Design Flexibility: This manufacturing process allows designers to play around various styles and patterns. Its flexibility gives room for designing jewelry in various shapes and sizes.
- Accuracy: The precision of the wax model and step-by-step casting process (such as chasing & polishing) ensures that the final piece accurately replicates the original design.
- Material Versatility: Lost wax casting process jewelry accommodates various metals, including brass, bronze, silver, and gold. This offers multiple options to achieve the desired aesthetic and durability.
- Cost-effectiveness: Lost wax casting is economical for manufacturing jewelry pieces with the same design. The mold can be used to produce thousands of the desired jewelry.
Disadvantages of Jewelry Lost Wax Investment Casting
- Size Limitation: The process can be tedious and time-consuming for larger items. Big jewelry pieces can be challenging to manage and may even require additional equipment.
- Surface Imperfection: The jewelry doesn’t always come out with a smooth surface. You might experience:
- Excessive surface roughness: A mistake in the casting process can result in excessive surface roughness, which will require extensive finishing to smoothen.
- Unexpected surface irregularities: Sometimes, the surfaces may suffer from blemishes that were caused by air bubbles during the casting process or particles in the molten metal.
- Inappropriate surface color: Variations in temperature and metal purity during the casting process can impact the color of the jewelry. Some parts may appear deeper than others.
- Porosity: During the casting process, tiny air pockets can form within the metal, thereby compromising the jewelry’s strength and causing cracks over time.
- Incomplete Casting: This happens when the mold is not designed accurately or when the molten metal doesn’t fill up the mold. The final piece ends up having missing parts or defects.
Application of Lost Wax Casting Jewelry with Digital Technologies
Lost wax casting is no doubt an ancient method of making jewelry. But it can be integrated with digital technologies like 3D jewelry design and CAD modeling to produce a more accurate and durable piece.
- 3D Printer: 3D jewelry design has revolutionized the lost wax casting process by enabling the creation of highly detailed wax models. It uses digital files to produce physical models layer by layer. 3D printer offers unmatched precision, allowing for the manufacturing of complex designs that would be difficult to achieve by hand carving. It also speeds up the design process, reducing the time and labor needed for most especially large pieces.
- CAD Software: Computer-Aided Design (CAD) software can be used to create accurate digital models of your jewelry designs. Instead of spending a lot of time crafting the wax model, the CAD software allows designers to visualize and modify their designs. It makes room for easy alterations and iterations, which guarantees that the final piece won’t have any defects.
Conclusion
Lost wax casting jewelry is a remarkable technique used for making both simple and complex pieces. While it has many advantages, it also has its shortcomings. But with the application of digital technologies like 3D printers and CAD software, you will have accurately designed jewelry with no defects.